February 2018 - In 1969, the American Welding Society celebrated its 50th anniversary at the annual Welding Show with a juxtaposition of old and new technologies, including displays of old welding machines, torches and positioners next to exhibitors showcasing the latest welding developments, such as plasma needle arc welding, a self-igniting air propane torch, a new welding/surface oscillator and a modern MIG gun Cablehoz design from Tweco.
Today, Tweco is part of ESAB, which builds welding and cutting equipment and consumables. Based in Annapolis Junction, Maryland, the brand still offers an enhanced version of that MIG gun rolled out in 1969—the Tweco Classic Numbered Series. Because welders have been dedicated to Tweco products for decades, the company reaches out to these experienced users for input when developing new products.
User feedback has resulted in improved, simpler front-end consumables for the Spray Master and Tweco Classic Number Series MIG guns featuring Velocity MIG welding consumables. Velocity consumables have a design that requires no tools and eliminates problems with threads.
Typical MIG consumables have two sets of threads, and many have three. According to welders, achieving smooth arc performance requires reducing the number of connections because each connection is a chance for poor conductivity.
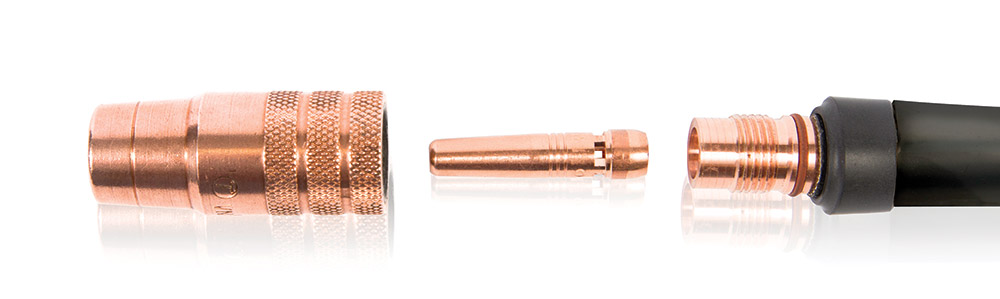
The new Velocity nozzle features a heavy-duty, high-temperature resin and a molded insert that enables the nozzle to screw directly on to the threads machined on the conductor tube. In addition to better securing the nozzle, this design reduces the operating temperature of both the nozzle and the conductor tube. To reduce the effect of reflective heat, the conductor tube features a high-temperature silicon tube covering, which also protects the jacket from impact and helps extend the conductor tube life.
Velocity consumables feature threadless, “drop-in style” contact tips and integrate the contact tip seating area directly into the conductor tube. In the medium- and heavy-duty Velocity consumables, the shielding gas flows from the conductor tube through four ports machined into the base of the contact tip. This simplified design eliminates the gas diffuser and enables the shielding gas to keep the tip up to 30 percent cooler.
According to ESAB, because Velocity MIG consumables run cooler, they can improve parts life by up to 500 percent or more in gas shielded flux-cored, spray transfer and pulsed spray transfer applications. In short-circuit MIG applications, Velocity consumables typically last two to three times longer than conventional consumables, the company claims.
A cooler tip also reduces the ability for spatter to stick. As a result, the tip needs less cleaning, and any spatter that adheres is easier to remove. Further, spatter generally collects on one part, the nozzle, as opposed to three parts on conventional MIG front ends.
“The drop-in style tip also eliminates the hassle associated with burn backs. There’s no need to use vise grips or welpers when the electrode fuses inside the tip,” says Jeff Henderson, ESAB’s global business manager for torches and Exothermic Cutting Systems.
He notes that good thermal management of front-end consumables extends consumable life and optimizes the electric and thermal conductive path, which greatly influences MIG gun performance.
“The updated Velocity design directly addresses heat-related issues by reducing consumable count, improving thermal conductivity and lowering operating temperature. As a result, updated Velocity consumables stay cooler, last longer, produce a more stable weld puddle and improve overall weld efficiency.”
ESAB Welding and Cutting Products
Florence, South Carolina
800/ESAB-123