October 2016 - In 1891, electrical engineer and inventor Elihu Thomson had this to say about arc welding: “It is not my present purpose to deal with any of these arc methods of electric metal-work. Their practicability is doubtful. So far as is known to the author, there are no existing instances of the use in practice of the electric arc for welding.” The findings of a 2015 report released by Transparency Market Research might surprise Professor Thomson.
The global welding products market is expected to reach U.S. $23.8 billion by 2020. In 2013, arc welding commanded just under 40 percent market share of the welding products industry taking the lead over resistance welding, oxy-fuel welding, laser beam welding and other methods. Among notable welding consumables, stick electrodes represented the largest product segment with a market share of more than 40 percent in 2013. Solid gas metal arc wires comprise the second-largest market segment. Flux-cored wires, SAW wires and fluxes represented smaller growth areas for welding products.
Arc welding is one of several fusion processes for joining metals and is widely used in the automotive, power generation and construction industries. Productivity, quality and safety/regulatory requirements are fueling the impetus for arc welding consumables development among automakers and manufacturers as well as pipe mills and pipelines operating in corrosive and abrasive environments.
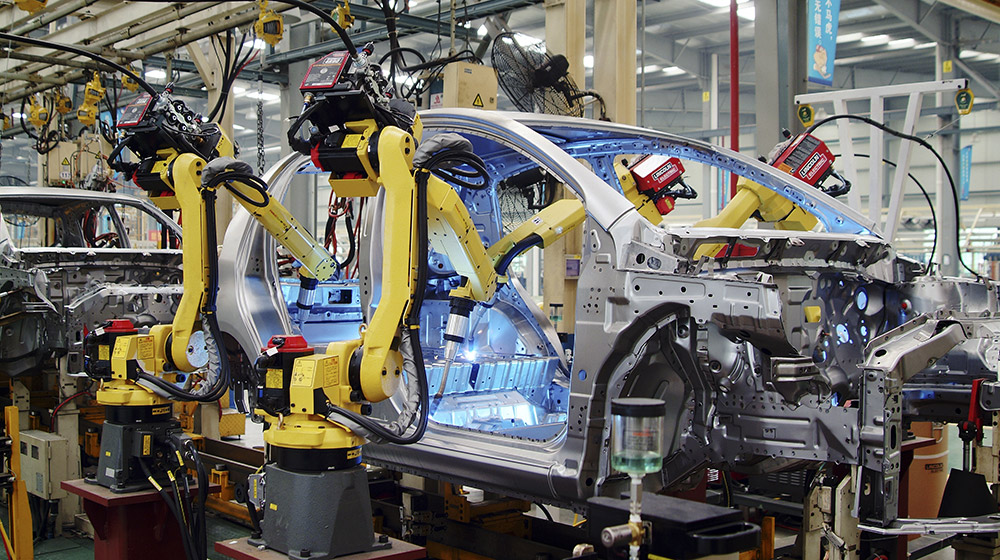
Forecast
Lincoln Electric Co., based in Cleveland, Ohio, is monitoring these trends along with the push for automated welding and cutting capabilities over manual processes and the escalating adoption of higher strength materials by manufacturers. The company has adapted its engineering ingenuity to create consumables and processes that manufacturers can use whether it’s on a vehicle assembly line or in the recesses of a subsea work site.
“We’ve grown from being a mild steel company to a multi-metal solutions provider,” says Bruce Chantry, director of marketing, North America for Lincoln Electric.
“Productivity is a big driver,” says Badri Narayanan, director of consumable R&D for Lincoln Electric. He points to the challenges automakers face to meet Corporate Average Fuel Economy (CAFE) standards to raise the combined average fuel efficiency of new cars and trucks to 54.5 miles per gallon by 2025. This year the target moves from 27.5 mpg to 37.8 mpg. The truck standard must move from 23.5 to 28.8 mpg. The need for lighter weight materials and higher productivity means welders are working with materials like aluminum and/or increasingly higher strength steels.
“Weight reduction can be achieved by a material change or by material thickness,” says Narayanan. “However, when you consider aluminum you have to look at its material properties. And if you are looking at joining aluminum to steel, you have to come up with a process that can handle the differences in material properties between aluminum and steel.”
Galvanized steel is also appealing in the race to reduce weight. Each material requires different welding methods. But it can be a hard goal to reach if a worker is welding galvanized steel with conventional processes. In the past, manufacturers had to choose between weld appearance, weld travel speeds or good X-ray quality. “But that’s no longer the case,” says Chantry.
Light weighting cars has been a trend for some time now, he continues. “But the low-hanging fruit has already been picked. All the fat has been cut off the bone. Carmakers are asking ‘where do we go from here to meet that objective?’ You have to take weight from the material and still meet mechanical requirements for productivity and quality—and, of course, safety.”
Problem solving
Lincoln Electric’s Process Z allows fabricators to weld galvanized material without sacrificing quality. Metalshield Z gas-shielded metal-cored wire—combined with Lincoln Electric’s patent pending Rapid Z waveform technology —allows welders to minimize internal porosity for defect-free welds. Minimal silicate and spatter can eliminate post-weld prep.
“We’re able to research and develop solutions that solve the difficult problems,” Chantry explains. “Often it means going to the drawing board to create a machine or waveform, consumables and software that can all work together. Compared to 15 years ago, welding equipment today can do amazing things from a performance standpoint. But it takes more than just the equipment, and when it comes to consumables, it can sometimes be a little like taking a race car and putting conventional street tires on it. The car can still race, but not at the level it was designed for. With welding operations, more often than not, we don’t know what kind of consumables they are using. We believe it’s the combination of the two that provides the best result. We know how our consumables will perform, and we can optimize the equipment based on that data to give the best total result.”
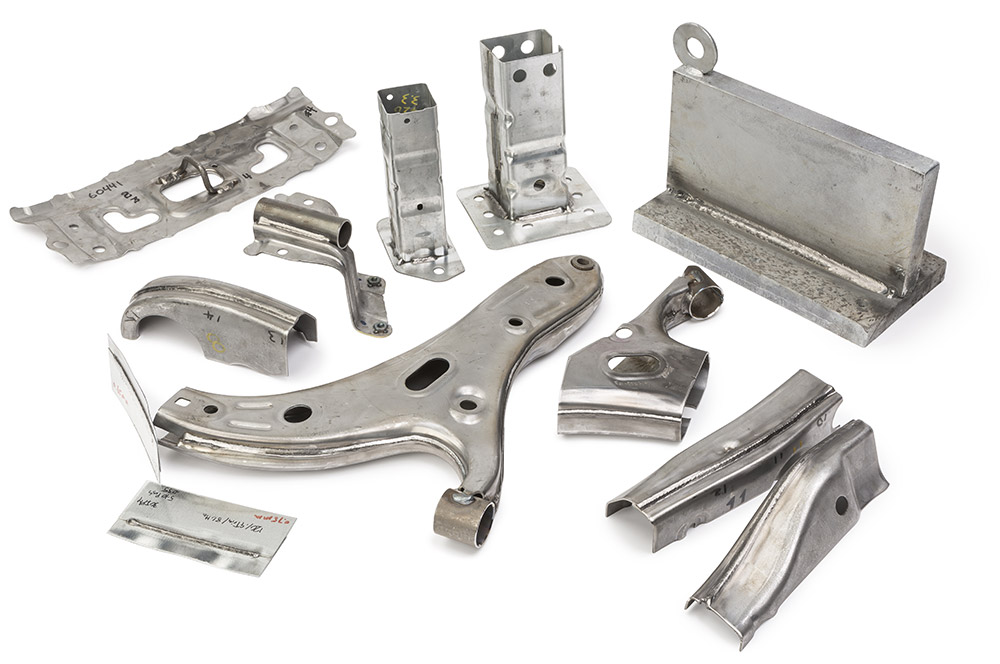
Tailor made
Lincoln Electric’s Power Wave products, enabled by Waveform Control Technology, have changed the way customers choose equipment. Power Wave systems support many different processes and materials, provide more than 80 different weld modes, and the ability to tweak or create new welding programs when needed. Power Wave solutions are available for semiautomatic, hard automation or robotic solutions.
Lincoln Electric tailors products for multiple industries. In cross-country pipeline welding, numerous factors can impact a welding operation and the consumables required. Consequently, an electrode’s design and the consistency of that design are critical to ensuring uniform operation of the electrode and the weld deposit.
“Take stick electrodes for example,” says Lisa Byall, portfolio manager-consumables for Lincoln Electric. “The chemistry of the weld deposit is directly related to the chemicals used in the coating. But there are variations of these chemicals available worldwide that each have different properties and performance characteristics. It’s crucial to find sustainable sources for these materials. We do a good job of analyzing raw materials to make sure performance isn’t negatively affected when we change supply sources. Strength requirements and codes can also change. One clear example of how Lincoln Electric tailors products for applications is the design philosophy behind Pipeliner Arc 80.”
Pipeliner Arc 80 is a stick electrode designed specifically for the cross-country pipeline industry that provides welders with a clear puddle that is easy to see and easy to manipulate. Fast-freezing slag gives the welder more control, making it possible to complete more pipe joints during a work shift while minimizing repairs.
“We partnered with pipeline welders during the development of this product to ensure it met their critical requirements,” says Byall.
In commercial markets, Lincoln Electric is seeing a transition from slower welding processes, like stick, to semi-automatic and automatic wire-based processes. As welding becomes more critical so does the need to control as many variables as possible, including training needs.
“One of the biggest challenges we’re seeing is that the average age of experienced welders is mid-50s,” says Byall. “Younger welders don’t have the same experience level. Training and development have to be provided.”
According to Chantry, wire-based processes can make operating welding equipment easier, but it still requires a practiced hand, or educated operator, to truly reap the benefits.
“Manual welding requires an operator with dexterity,” he says. “The things people used to do with their hands, kids are now doing virtually in a digital world. We have had to implement virtual training to help prospective employees—many of whom are gamers—relate and to learn the muscle memory needed for welding. Automation helps ensure a good weld, but the best operators of automatic welding equipment are those with solid experience in manual welding. They know how to look at the puddle and weld and adjust the procedures if needed.”
For pipe mill manufacturing applications, the company has developed solutions like Lincolnweld Emergence, a non-copper-coated submerged arc wire for pipe seam welding. The wire is treated with a proprietary surface that protects material while providing the same performance as copper coated wires in the same alloy class.
“With pipe seam submerged arc welding, there is no margin for error,” Narayanan explains. “Processing flaws can mean costly repairs or scrap. By eliminating surface copper, the risk for weld contamination is reduced.”
Selecting the right contact tip and wire is also critical. Inadequate contact tips can result in excessive downtime and lost production. Emergence wire has demonstrated its ability to double the life of contact tips. Wire composition also makes it easy to requalify for welding procedures that are controlled by classification.
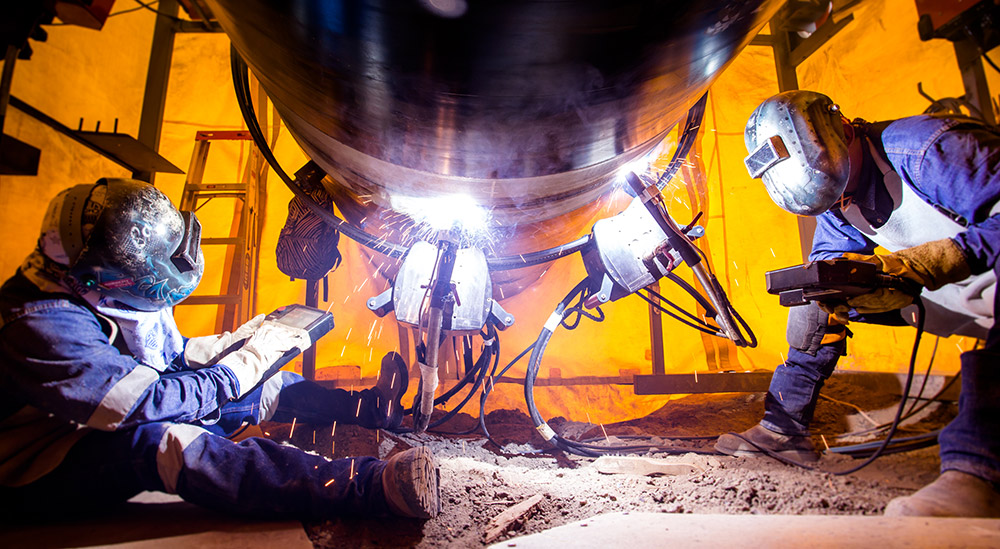
Testing performance
“Extreme environments test the performance of materials as well,” says Narayanan. The Weartech line of products is used to overlay or coat materials that need to be protected from harsh surroundings that are subjected to erosion, corrosion and abrasion. Weartech products are suited to a variety of welding processes for applications ranging from the oil and gas, power generation and pulp and paper industries to mining, offshore and marine markets.
Regardless of the job, manufacturers are looking for higher productivity, higher quality, greater safety measures and lower operational costs.
“Almost anyone can develop and manufacture a welding consumable,” says Chantry. “It takes best practices from start to finish to create consumables that can deliver consistent performance and welds time after time. Market demands are taking us in new directions that include the exploration of new materials with more challenging mechanical requirements. The operator just wants a consumable that works the same, day in and day out, and can deliver an attractive weld.”
At the end of the day, Lincoln Electric understands that it is a balancing act between operator skill, productivity requirements and quality expectations.
Lincoln Electric
Cleveland
216/481-8100