When evaluating total cost of ownership, premium dust collector filters actually cost less
July/August 2019 - Metal fabricators looking to purchase replacement filters for their cartridge dust collectors should look beyond sticker price to determine the best value. When comparison shopping, dust collector filters from different manufacturers might look equal because they offer the same filtration efficiency and meet the same filter media requirements. However, when considering the performance attributes and durability of the filters, premium dust collector filters often cost far less over time than standard filters.
Choosing the right cartridge dust collector filters can have a big impact on the total cost and performance of a dust collection system. Premium extended-life cartridge filters reduce changeout frequency and save on replacement, maintenance and disposal costs. In fact, long-life premium cartridge filters can operate for years between changeouts, depending on the application.
On the other hand, inexpensive aftermarket filters can malfunction rapidly—sometimes in mere weeks. For example, when low-cost filters are used in Camfil dust collectors, they often can’t withstand the power of the pulse cleaning system. The filter paper can come unglued, flanges can warp, seals can rupture and filters can come off track, in addition to other performance failures. Beyond creating a mess, failed filters expel the collected dust back into the facility, causing a health risk for employees, contaminating products and damaging equipment.
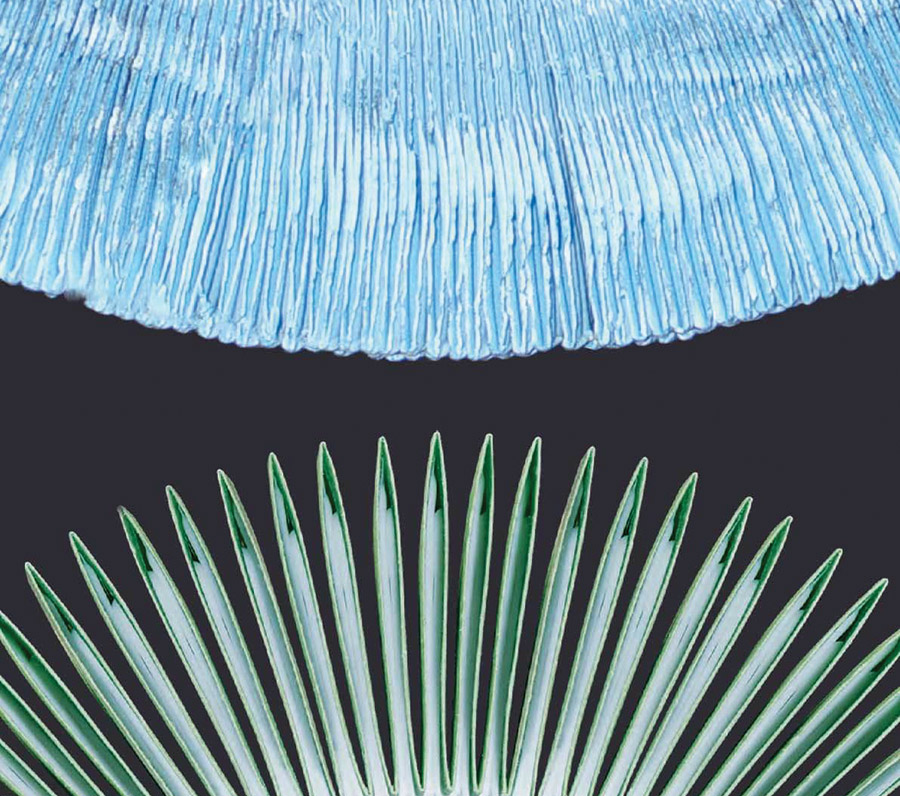
Total cost of ownership
When choosing a dust collector filter, calculating total cost of ownership (TCO) provides the most economical and energy-efficient choice. For example, a filter with a lower initial price may end up costing thousands of dollars a year in energy and operating expenses. Similar to life-cycle costing, TCO is a step-by-step evaluation of the four main components of filter cost: energy, consumables, maintenance and disposal.
Energy costs: When calculating TCO, first consider the amount of energy required to operate the dust collector, including electrical costs, compressed air usage and CO2 emissions. The system’s fan or blower uses the most energy because that is what moves air through the system. Differential pressure losses are directly proportional to the amount of air moved, which, in turn, is directly proportional to the cost of energy used.
Filters use more energy in the early stages of service life and less in the final stages. When filters are clean and differential pressure is at its lowest, more air blows through the system than required, which wastes energy. As filters become loaded with dust, the static pressure increases, and less air is moved as a result.
Cost of consumables: Consumable components of a dust collector are the items that are replaced periodically throughout the life of the equipment. The priciest consumables are the filter cartridges, so purchasing more expensive filters that last much longer actually cost less in the long run.
Maintenance costs: Maintenance costs include the time it takes to service the equipment. This includes the cost of having replacement filters delivered to the facility and the cost of carrying this inventory, the cost of labor required for maintenance personnel to change filters, and the downtime costs due to stopping operation of the collector for a filter change.
Disposal costs: Don’t forget the cost of disposing of the filters. Depending upon the type of material being filtered, it can be very costly to dispose of filters laden with process dust, especially if it is hazardous.

Boosting long-term value
Many metal fabricators believe that the more media a filter contains, the longer it will last. This is a common misconception. Actually, the total square footage of media contained in a filter is not as important as the square footage of usable media. Many filters have media packed so tightly into the cartridge that most of it is not available for filtering. When the pleats of the filter media are tightly packed, the reverse pulse cleaning system of the dust collector will not eject the dust that has settled between the pleats. Also, tightly packed pleats increase the resistance of the air through the filters and diminish airflow, using more energy and requiring more maintenance to recover performance.
The key is to use a wide pleat design where 100 percent of the media is usable. This design improves airflow through the filter, which reduces pressure drop and saves energy. Open-pleat filters also respond well to pulse-cleaning and use less compressed air than some other filter designs, saving more energy and lasting longer, which lowers replacement and disposal costs. A wide-pleat filter allows the collected dust to release from the filter, keeping the resistance lower through the filter for a longer time.
Dust collection systems are a major capital investment. Making an informed decision can improve the overall efficiency of a dust collection system and lower energy and operating expenses when capturing hazardous and nuisance metal dusts.
Camfil APC
Jonesboro, Arkansas
800/479-6801