Above: Enduro-Flex Stainless flap discs reduce costs by providing a consistent finish in one step.
Metals used in pharmaceutical equipment must meet rigorous standards
February 2019 - At first glance, the metal fabrication sector seems to be a world away from the pharmaceutical industry, yet both share common ground with their mutual appreciation for the versatility and safety of stainless steel. Industrial V-blenders, for example, are typically manufactured from grades 304 and 316 stainless steel. The device’s profile is essentially that of a large, angled (V-shaped) tube with an outside corner and an inside corner.
Circular tubing, square tubing and welded sheets are components that figure prominently not only in the pharmaceutic processing equipment spheres but also in countless other markets. V-blenders are used for dry powder blending in process industries such as drug compounding, food and beverage production and chemical manufacturing.
Pharmaceutical equipment manufacturers are key consumers of grade 300-series austenitic stainless steels, mainly because of the materials’ resistance to contamination once cleaned and polished. A perfect surface finish improves cleanability, which means equipment and systems can be maintained to increasingly stringent levels of sterility.
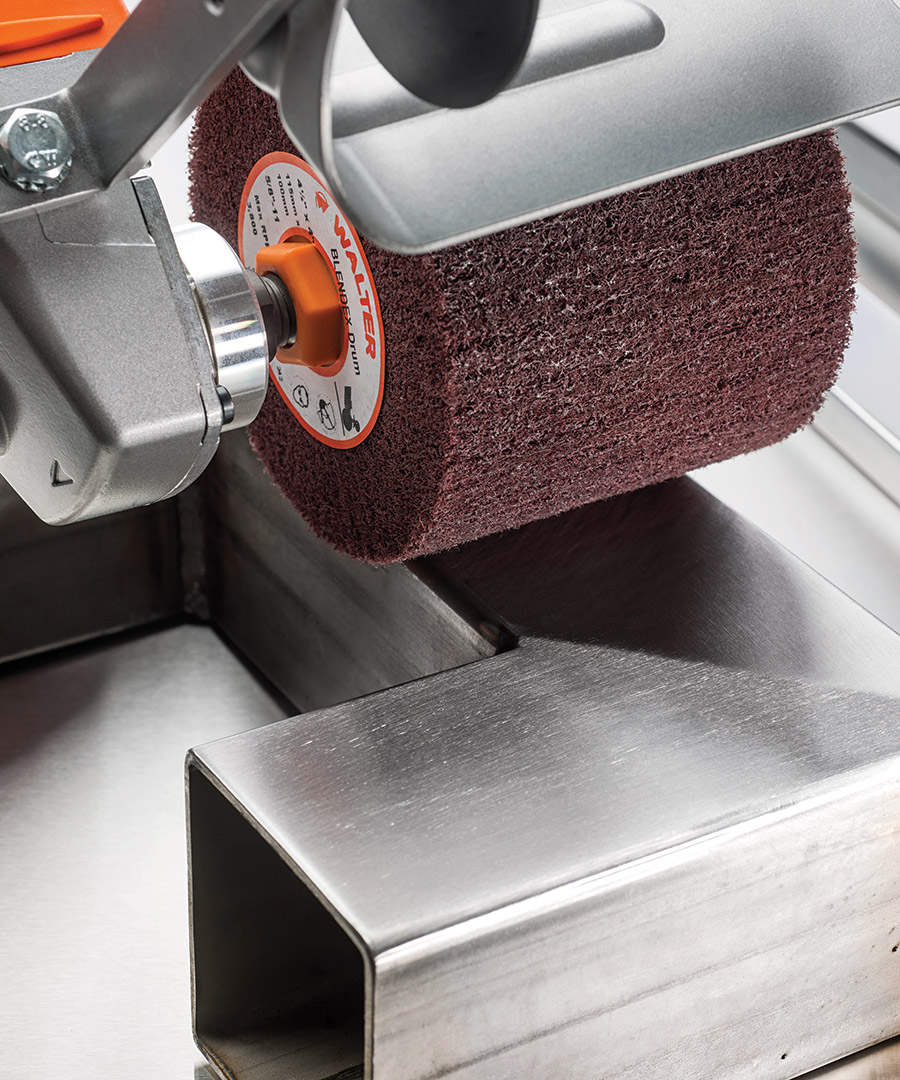
Combat contamination
The medical industry has long known the impact and importance of surface finishes for high-purity systems, such as biopharmaceutical manufacturing equipment. There is virtually no margin for error because this industry contributes to quality of life for millions of people.
Highly polished stainless steels are non-reactive, non-additive, non-absorptive and non-corrosive. Low-carbon stainless steels are resistant to hostile chemical compounds and are used when products require maximum levels of containment against contamination, as in drug development and compounding.
For example, grade 304L is a low-carbon variation of grade 304 with slightly higher corrosion resistance. It is sometimes specified for welding heavy sections in pharmaceutics processing machines.
The advantage of using stainless steel for pharmaceutic compounding is its inherent resistance to contamination, which, in our industry, is generalized as “corrosion.” But stainless steel doesn’t become “pharma ready” all on its own. For example, when Walter Surface Technologies first developed its Surfox weld cleaning systems and Line Mate III finishing systems, the company was responding to market demand for faster, cleaner processing technologies.
Achieve smooth surfaces
Surface roughness standards of stainless steels used by the pharma industry are rigorous. Roughness averages (Ra)—the average height between the metal’s surface peaks and valleys—must fall between 12 and 25 micro-inches to inhibit bacteria. To help fabricators meet these standards, Walter developed its Enduro-Flex Stainless flap discs.
Made with a formulation free of iron, sulfur and chlorine, these “flappers” have the fastest removal rate on stainless steel, which drives productivity, cuts operation costs and enables consistent surface finishes. Walter’s Blendex and Quick-Step finishing discs were developed with the same benefits: fewer steps toward the end goal of medical-grade (and other sectors) finished stainless steel products.
Because pharma is a high-purity industry, electrochemical weld cleaning literally shines as a key technology. This anodic leveling process contributes to clean, smooth, sterilizable surfaces by leveling micro-peaks and valleys in stainless steel finishes.
Walter’s Surfox weld cleaning systems, which clean and, more importantly, passivate stainless steel welds, are highly effective for these applications. Surfox promotes the formation of a uniform and durable chromium-oxide passive layer to protect stainless steel against corrosion.
There are key advantages to working with stainless steel, but it’s not without its challenges. Stainless is three times more expensive than steel, and finishing takes significant time and requires more skilled labor. This makes working with stainless even more expensive. Reducing the number of steps in the finishing process is crucial. Workers should be equipped with the proper tools and familiar with the latest technologies.
Whether a workpiece is destined to life in a pharmaceutical factory, dairy, brewery or otherwise, it has to be the best it can be. Walter offers safe, efficient and expert solutions to do so, from start to finish.
Stainless steels play a vital role in pharmaceutical applications
More than 200 different grades of stainless steel possess properties to suit various manufacturing needs and product protection requirements.
For pharmaceutical hygiene products, grades 304 and 316L are commonly chosen for their corrosion-resistance. Within the 300 series, grade 304 is known as “surgical” steel. It’s used mainly in pharmaceutical, dairy and brewery production equipment. Grade 316 contains molybdenum and a higher nickel content (10 percent) than grade 304. In conjunction with chromium, molybdenum provides a high resistance to permeation by most chemicals and an increased resistance to chloride corrosion when compared with grade 304.
The most common type of stainless steel used in the pharmaceutical industry is grade 316L. Corrosion resistance is the same as for 316, but its low carbon content helps avoid sensitization corrosion in welding. Grade 316L is also often specified in pharma installations to prevent excessive metallic contamination of pharmaceutical products. As a general rule, grade 316L is used in all “product contact” applications, and grade 304 is used in “non-contact” applications.
Walter Surface Technologies
Windsor, Connecticut
860/298-1100